Exploring the Art and Science of Wax Molding Jewelry

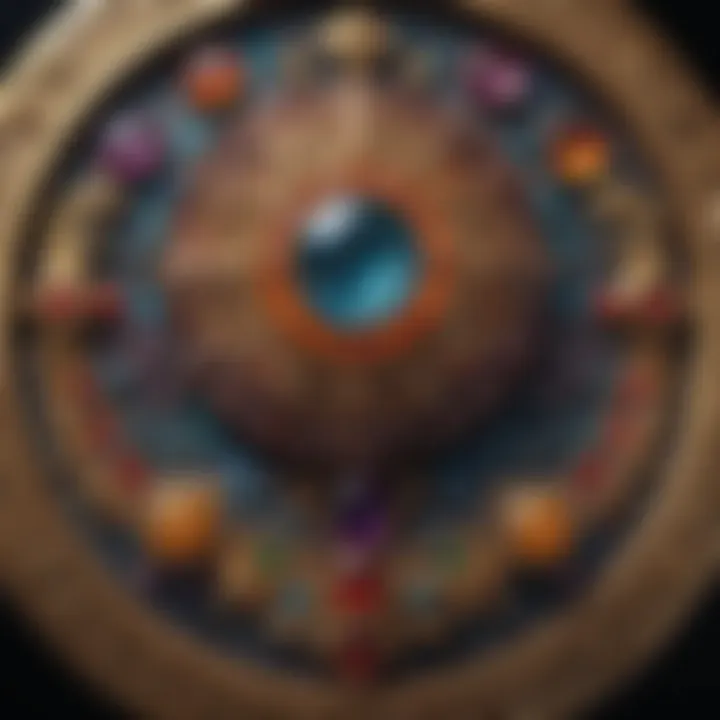
Intro
Welcome to the intricate world of wax molding jewelry, where artistry meets scientific precision. This craft bridges the gap between traditional metalworking and contemporary design, bringing to life extraordinary pieces that blend creativity and functionality. Wax molding, a method that has stood the test of time, allows artisans to conceptualize their visions with remarkable detail and accuracy. The ability to manipulate wax, alongside a deep understanding of the materials used, positions this technique as a keystone in the jewelry-making domain.
As we dive further, we'll explore various facets of this craft, ultimately shedding light on its significance in today’s jewelry industry. The insights shared here will aim to enrich the understanding of gemstone enthusiasts, collectors, and jewelry designers alike.
Let’s start our exploration by discussing the foundational components that contribute to this engaging art form.
Preamble to Wax Molding
Understanding wax molding is essential for anyone who appreciates the intricate relationship between art and craftsmanship, particularly in jewelry making. This process serves as a bridge connecting creative design and the technical execution needed to produce stunning pieces. Furthermore, it allows for the fine detailing that distinguishes high-quality jewelry from the mass-produced items that flood the market today. In short, mastering wax molding opens up countless avenues for designers, providing a unique way to express their artistic vision.
Definition of Wax Molding
Wax molding is the practice of using wax to create a model or prototype that will eventually be replicated in a more durable material, typically metal. This process involves shaping and carving wax, which is later cast into a final product. Due to its flexibility and ease of manipulation, various types of wax can be used, each catering to different aspects of the design process. By utilizing this method, artisans can achieve impressive levels of detail and precision—qualities that are often sought after in bespoke jewelry pieces.
Historical Overview
The roots of wax molding can be traced back thousands of years, revealing its significant role in the development of jewelry making. This historical context helps to provide insight into the current methodologies and philosophies that guide modern artisans.
Ancient Techniques
In ancient civilizations, the techniques of wax molding served as a crucial method for creating intricate jewelry. Many cultures, from the Egyptians to the Greeks, used beeswax and other natural substances to craft models of jewelry pieces. The key characteristic of these ancient techniques was their reliance on simple tools and the artisans' skills.
Utilizing hand-carved wax, artisans were able to achieve remarkable detail, which was often essential in cultural and ritualistic works. The beneficial choice in this method pointed toward its accessibility; it allowed a wider range of artisans to engage in the craft freely.
However, these approaches had their challenges. In some cases, the wax would melt too quickly under heating or not hold up under pressure, leading to imperfections in the final products. Still, the use of wax has become a historic hallmark, with this ancient art form holding lasting influence today.
Evolution Over Time
As time passed, the techniques associated with wax molding jewelry evolved significantly, influenced by advancements in material science as well as artistic trends. The key characteristic of this evolution is the introduction of synthetic waxes that offer advantages over natural wax. These modern materials provide greater durability and can withstand a wider range of temperatures without deforming.
This evolution, in a sense, fuels the continuous growth of the craft. Designs can be more ambitious, allowing for a broader creative freedom that generations past could only dream of. Still, it’s essential to recognize that with increased capabilities come new challenges as well. Artisans today must navigate not just the technical aspects of the materials but also the environmental considerations that come with using synthetic waxes. Nevertheless, the journey from ancient methods to present-day techniques stands testament to the enduring charm of wax molding in the jewelry industry.
The Role of Wax in Jewelry Making
Wax's importance in jewelry making can't be overstated. It serves not just as a material but as the very foundation upon which intricate designs and creative visions come to life. Craftsmanship in this field hinges on the adaptability and performance of wax in molding techniques. Through various forms of wax, artisans can achieve the precision and detail required for stunning jewelry pieces. Whether it's a delicate pendant or an elaborate ring, the capacity to translate ideas into tangible models through wax means artists can push their creative boundaries while still maintaining a level of practical effectiveness.
Types of Wax Used
In the realm of wax molding, three primary types find their place: carving wax, casting wax, and injection wax. Each has its unique characteristics that make them suitable for various applications within jewelry making.
Carving Wax
Carving wax is often viewed as the artist's clay in the jewelry industry. It's primarily used for creating the original model that will later be transformed into metal. This type of wax is softer and can be manipulated easily, allowing designers to express their ideas with great fluidity during the modeling phase. A standout feature of carving wax is its ability to hold fine details during the carving process, which is crucial for producing elaborate designs. However, as beneficial as it is for detailed work, its softness means that it can be prone to dents and scratches if handled too roughly.
Casting Wax
Casting wax plays a pivotal role in the actual casting process. This rigid type of wax is designed to withstand the heat and pressure of the metal casting process. Its key characteristic lies in its melting point, which is tailored to assure that when heated, it leaves a clean impression in the mold. A unique feature of casting wax is its ability to reproduce very precise forms, which is essential for creating complex jewelry designs. On the flip side, its stiffness can be a double-edged sword, as it makes carving more challenging compared to softer types.
Injection Wax
Lastly, injection wax is notable for its use in high-volume production. This wax is injected into molds under pressure, allowing for an excellent reproduction of intricate details. One of its most compelling features is its consistency and uniformity, making it incredibly reliable for larger production runs. The speed of this process is another advantage, as it significantly reduces manufacturing time. However, the trade-off often comes in the form of higher initial equipment costs for injection setups, making it less accessible for smaller artisans or hobbyists.
Advantages of Wax Molding
Wax molding stands out not merely for its versatility in producing designs but also for the numerous advantages it offers to artisans.
Precision
One of the most lauded benefits of wax molding is the precision it provides. The ability to create highly detailed models allows jewelry makers to experiment with designs that might otherwise be impractical in solid materials. The precision of the wax model directly impacts the final metal product, where imperfections in the initial mold can lead to costly mistakes in the final piece. This precision is a critical element in achieving the desired aesthetic results, especially for fine jewelry.
Versatility
Versatility is a hallmark of wax as a medium. Jewelers can easily transition from one design concept to another without losing momentum in the creative process. Whether it involves creating elaborate rings or simple pendants, wax allows for diverse artistic expression. This adaptability can benefit makers extensively, enabling them to respond to varying client demands swiftly.
Cost-Effectiveness
Cost-effectiveness remains a major draw for many artisans. When compared to other methods, wax molding often presents a lower cost of entry. The materials needed for creating initial models are relatively inexpensive, coupled with the fact that wax can be reused and remelted. Thus, artisans can save on raw materials while still achieving quality outputs in their designs, leading to increased profitability and sustainability in their processes.
The Process of Wax Molding
The process of wax molding presents a comprehensive pathway for transforming creative ideas into tangible jewelry pieces. This phase of jewelry making delineates not only the technical aspects of how wax is manipulated, but also serves as a vital bridge between artistry and craftsmanship. Understanding this process is crucial because it highlights the ability of artisans to execute detailed designs with precision.
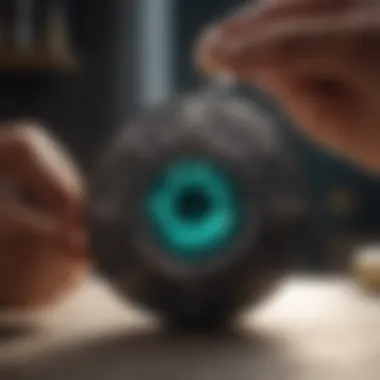
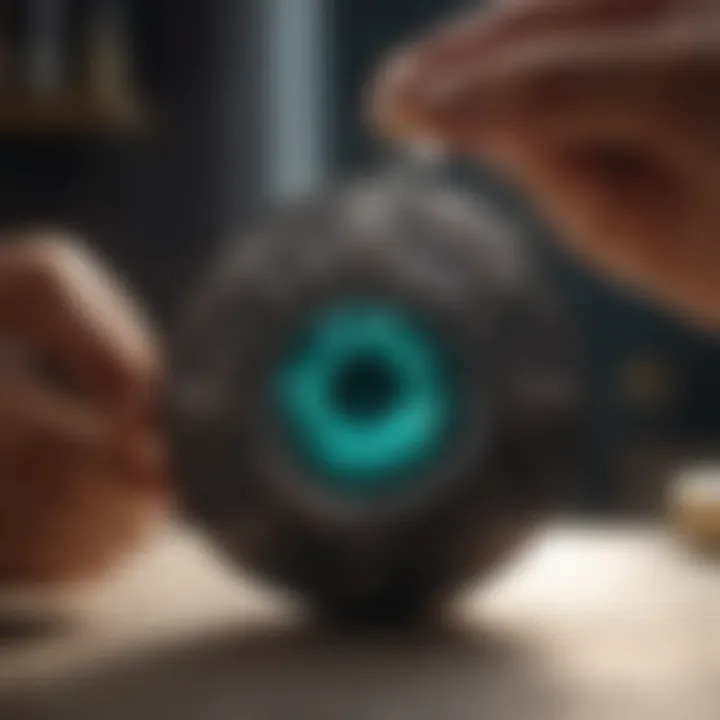
Creating the Wax Model
Creating a wax model serves as the cornerstone of the wax molding process. This step encapsulates various methods that contribute to the final form of the jewelry.
Initial Sketching
When initiating a project, initial sketching plays an integral role. It allows creators to visualize their concepts before any material is touched. This key characteristic of sketching is that it harnesses the power of imagination, serving as a guide for the entire design process. For instance, a simple doodle can evolve into an intricate pendant design. One unique feature is the ability to make quick changes during this stage; it's easy to erase and adjust before committing to wax. However, some might find that they spend too much time on sketches, potentially delaying the actual crafting.
Carving Techniques
Carving techniques are vital for turning wax blocks into beautiful models. They showcase the artisan's skill and creativity. This includes using tools like knives, chisels, or even dental tools to refine shapes and add intricate details. The benefit of employing traditional carving is the tactile connection it fosters between the artist and their work. The unique aspect lies in handcrafting, where nuances that a machine cannot replicate become a part of the piece. However, depending on the artisan’s skill level, there can be mistakes that might require considerable correction time.
Digital Wax Modeling
With advancements in technology, digital wax modeling has emerged as a revolutionary technique. This modern approach utilizes software to design intricate jewelry pieces with a precision that traditional methods sometimes struggle to achieve. The most appealing characteristic about digital modeling is the versatility it offers; designs can be manipulated easily, allowing for rapid prototyping. The ability to correct errors instantly is another significant advantage. Yet, reliance on technology might reduce the creative process's tactile and emotional aspects, which some artisans hold sacred.
Mold Making
Mold making is an essential process in wax molding, enabling the transformation of wax models into metal jewelry. Understanding this aspect helps elucidate how artisans replicate designs efficiently.
Types of Molds
In wax molding, there are primarily two types of molds used: soft molds and hard molds. Soft molds capture the detailed nuances of a wax model, while hard molds allow for multiple castings of the same piece. The benefit of soft molds is that they can reproduce intricate details without loss, making them a popular choice for artists focusing on detail. Conversely, hard molds offer durability and are preferred for production in larger quantities. One downside is that soft molds can wear out more quickly than hard ones.
Mold Preparation
Mold preparation is a crucial step that involves ensuring that the mold can properly receive and contain the molten metal. This involves cleaning, lining the mold, and sometimes the application of a release agent. A well-prepared mold is less prone to casting defects. The auccuracy in this preparation leads to a more seamless casting process, ultimately saving time and materials during production. However, the attention to detail required in this step may be daunting to those inexperienced with the intricacies of mold making.
Casting Process
The casting process is where the magic happens—merging the wax model and molten metal to create the final piece. The main characteristic of this process is how it brings the predetermined design to fruition. Many artisans regard this as the most exciting part of wax molding. A significant feature here is the choice of metal, which can greatly influence the final product's aesthetic and durability. While this technique can result in stunning pieces, there’s always a chance of miscast, which can lead to material wastage and additional costs.
Casting in Metal
Casting is a fascinating part of the wax molding process, involving transforming wax into metal creations. It comprises two significant casting methods that exert their own benefits and challenges.
Lost Wax Casting Method
The lost wax casting method is a time-honored technique that has been in practice for centuries. The beauty of this approach is that it captures every detail from the original wax model. This method is celebrated for its adaptability to various materials, including silver and gold. An advantage of lost wax casting is its ability to produce highly intricate designs that are often unachievable through mass production methods. However, the process can be labor-intensive and requires significant skill to ensure successful results.
Alternative Casting Techniques
Innovations have led to the rise of various alternative casting techniques that complement the traditional methods. Techniques like sand casting or investment casting offer different benefits at a potentially lower cost or enhanced efficiency. The advantage of these methods often lies in faster production times or the capability to create larger objects, which can appeal to certain markets in jewelry. Nonetheless, they might not replicate the fine details in the same way as lost wax, which some artists might view as a drawback.
Artistry and Design in Wax Molding
In the realm of wax molding, artistry and design play a crucial role in determining the aesthetic and functional appeal of the finished jewelry. The intersection of these two elements creates a canvas where creativity meets technical skill, allowing artisans to breathe life into their visions. From the initial concept to the final polish, every decision made in this phase not only affects the beauty of the piece but also its marketability and relevance in the jewelry landscape.
Creative Freedom
Sculptural Designs
Sculptural designs set wax-molded jewelry apart, making it not just an accessory but a statement piece. This style emphasizes bold forms and intricate details, resulting in creations that are visually striking. One of the major advantages of sculptural designs is their ability to convey a story or an emotion, offering the wearer a personal connection with the piece.
These designs often break free from traditional forms, embracing fluidity and organic shapes. Artisans can create anything from abstract geometric patterns to nature-inspired motifs. The unique feature here is how these pieces become conversation starters; their unconventional designs draw admiration and curiosity. However, it's worth noting that such intricate workmanship can also lead to higher production costs and longer creation times, sometimes making them a less favorable option for mass production.
Functional Jewelry
On the flip side, functional jewelry marries utility with artistry. This category focuses not only on beautiful aesthetics but also on the piece's wearability and practicality. Items like rings that can double as a pen or pendants that serve as a locket showcase innovative designs that appeal to a broader audience.
The key characteristic of functional jewelry is its dual purpose. It keeps the artisan's creative impulses alive while providing a useful object. This versatility makes functional pieces popular choices in contemporary jewelry. One unique aspect is that they often incorporate elements that enhance the usability without sacrificing style. However, an artist must carefully execute these designs so that neither function nor aesthetics suffer. This balance can sometimes prove challenging, requiring a thoughtful consideration of both elements.
Incorporating Gemstones
Settings in Wax Models
When integrating gemstones, settings in wax models play a pivotal role. This aspect focuses on how gemstones are incorporated into the design, directly affecting the overall appeal of the piece. A well-designed setting can highlight a stone's natural beauty and enhance the overall aesthetic of the jewelry.
Settings made in wax provide a degree of versatility that allows for intricate detailing and the perfect fit for each unique gemstone. The primary advantage here is the ability to customize settings that complement the specific characteristics of the stones, whether it’s a vibrant ruby or a sparkling diamond. However, on the downside, there can be challenges in ensuring that the wax model holds up during casting, which requires careful planning and execution.
Balancing Design and Stones
The concept of balancing design and stones is vital in the art of wax molding. It’s a dance of sorts where creativity and natural beauty come together harmoniously. This balance allows the design not to overshadow the stones but instead enhances their inherent qualities.
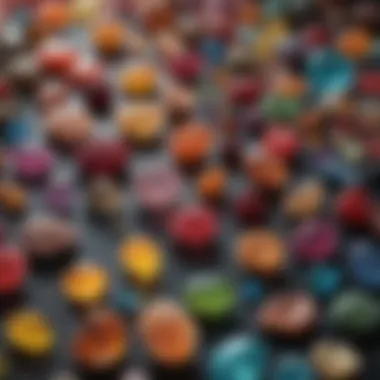
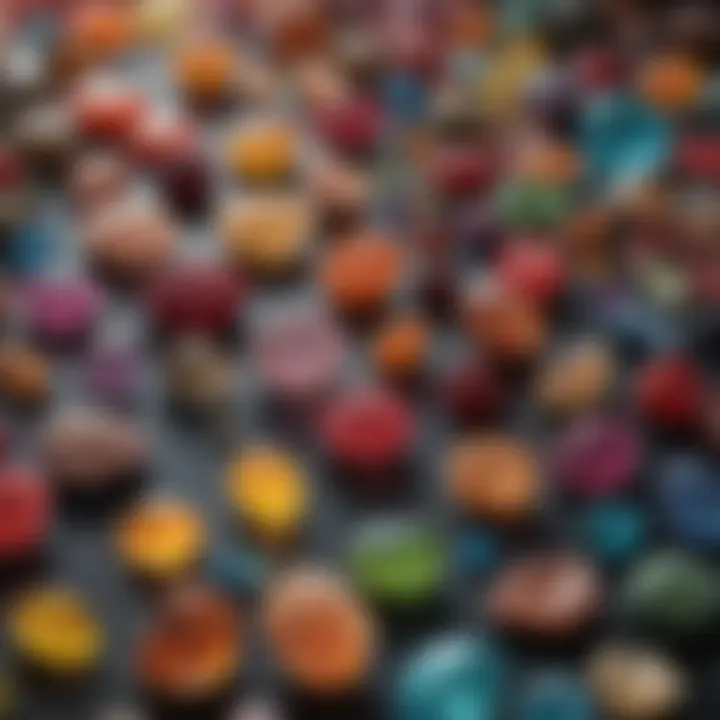
A well-executed balance between the design and the gemstones can amplify the allure of both. For instance, a delicate filigree can add depth to an otherwise simple piece, while a chunky gem might demand a more robust design. Unique to this balancing act is that it requires a keen eye and deep understanding of materials, as a poorly balanced piece can leave the overall design feeling mismatched. Ultimately, achieving that equilibrium can take a lot of practice but yields stunning results that captivate and maintain the essence of artistry in jewelry making.
Challenges in Wax Molding Jewelry
Navigating the world of wax molding for jewelry comes with its fair share of hurdles. While it's a captivating and intricate craft, the challenges faced by jewelers can sometimes feel like a weighty anchor. Understanding these challenges is essential not just for artisans but also for anyone interested in the craft. Grasping the pitfalls involved can equip jewelry makers to sidestep common errors and aim for excellence in their creations.
Common Pitfalls
In the realm of wax molding, there are two key areas where pitfalls tend to lurk: material limitations and technical difficulties. These aspects can deeply impact the final product, either creating opportunities for exquisite design or significant setbacks.
Material Limitations
Material selection plays an indispensable role in the quality of the jewelry. Certain wax types may not withstand high temperatures or detailed carving techniques, limiting creativity. For example, paraffin wax is popular for being economical and readily available, but its lower melting point can pose challenges when designs require precision during heating processes. Its fragility compared to other waxes makes transitional phases delicate. Essentially, the wax chosen dictates the boundaries of the design — great for beginners learning the ropes, but it can easily restrict more experienced artisans looking for detailed fidelity in their pieces.
Pros of material limitations include:
- Affordability: Low-cost wax can be sourced easily.
- Ease of use: Soft wax is beginner-friendly for intricate carvings.
However, the cons should not be overlooked:
- Durability: Waxes like paraffin can't hold up under high-pressure casting.
- Inflexibility: Once set, correcting flaws can be hard without risking the piece's integrity.
Technical Difficulties
Struggles with technology can rear their heads at different stages of the wax molding process. For example, improper temperature settings during wax pouring can spoil a creation before it even gets started. If the wax is too hot, the model may lose detail; too cold, and it can become difficult to mold. This tightrope dance can lead to frustrating errors very quickly.
The nature of how wax models are carved or printed directly influences the ease or difficulty faced by artisans. Many people favor the use of CNC machines or 3D printing for precision, but these tech-savvy methods require a keen understanding of both hardware and design software, which can lead to steep learning curves for some jewelers.
So, what are the advantages and downsides?
- Pros:
- Cons:
- Precision: Allows for detailed, accurate pieces that are harder to achieve manually.
- Efficiency: Technology speeds up the production process.
- Learning curve: New tech approaches can complicate the initial design-phase.
- Equipment costs: Investing in technology can be pricey and a barrier to entry for newcomers.
Quality Control
Once the initial step is completed, quality control becomes the linchpin in the process of wax molding jewelry. It's not just about creating; it’s about ensuring what is created meets standards that customers expect.
Assessing Wax Models
Monitoring the integrity of wax models is vital for preventing costly mistakes. Regular checks are needed during the modeling phase and before casting to ensure that the correct proportions and details are in place. It's almost expected in the industry that each model receives careful consideration. A thorough assessment can ultimately save a jeweler time and resources by identifying issues early on.
Key benefits of adept assessing include:
- Spotting errors: Identifying issues before the casting saves confusion later.
- Quality assurance: Regular checks give a sense of security for the expected output.
However, assessing can also present challenges:
- Time-consuming: Thorough checks may extend production timelines.
- Experience needed: Evaluating designs requires a trained eye to be effective.
Post-Casting Inspection
Once the casting is done, the importance of inspections becomes even more pronounced. At this juncture, identifying flaws in metal or structure is crucial as these could derail the entire piece’s potential sales success. Post-casting inspection allows artisans to examine the surface for imperfections, gouges, or issues that could compromise the design’s overall appeal.
By ensuring this final step is followed, jewelers are likely to foster customer satisfaction and trust. Key aspects include:
- Enhanced quality control: Minimized risk of selling inferior products.
- Customer loyalty: Investing in quality ensures returning clients.
The drawbacks in this process can include:
- Labor-intensive: The inspection can be meticulous and require extensive effort.
- Cost implications: Additional inspection processes mean more resources spent, which can impact profit margins.
"The balancing act of art and science requires not only creativity but also precision — it’s the delicate dance of molding that makes each piece not just jewelry but a fragment of the artisan’s soul."
In the realm of wax molding for jewelry, identifying challenges is the first step towards mastering the craft. Acknowledging limitations in materials and address technical difficulties will enhance creativity and innovation. Ready to refine your skills? Discovering ways to mitigate issues invites higher standards and craftsmanship in a field that always remains a blend of art and artistry.
Innovations in Wax Molding Techniques
Innovations in wax molding techniques represent a pivotal shift in how jewelers bring their ideas to life. As technology advances and creative minds look for new methods, the integration of tech into traditional practices shows how craftsmanship evolves while maintaining its artisanal roots. These advancements are not just about efficiency; they enhance precision, expand design possibilities, and promote a more sustainable approach to jewelry making.
Technology Integration
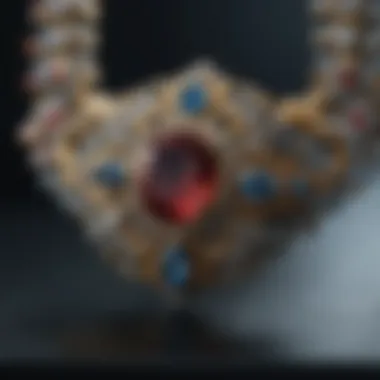
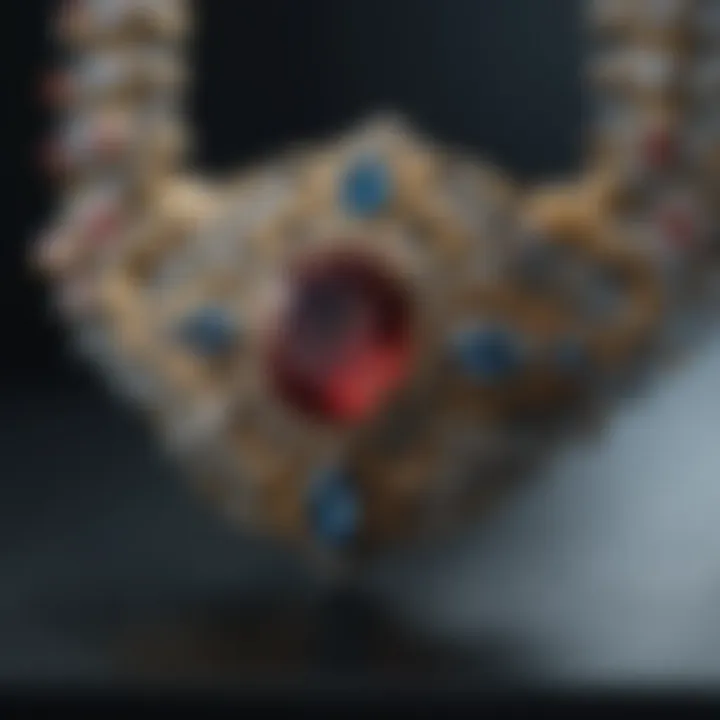
3D Printing
3D printing has emerged as a game-changer in the world of jewelry making. This technology enables artisans to create intricate designs that were once constrained by manual limitations. What sets 3D printing apart is its ability to produce complex geometries that can introduce both elegance and functionality into a piece. The printers utilize different materials, allowing for a variety of finishes and styles.
The unique characteristic here is the layer-by-layer construction that yields a higher level of precision compared to traditional methods. Many jewelers have opted for this method due to its adaptability and speed. One notable benefit is how quickly a design can go from concept to prototype, which can be crucial for keeping up with market trends.
However, this innovation is not without its downsides. The initial cost of setting up 3D printing technology can be a barrier, particularly for emerging artisans. Also, understanding the intricacies of designing for 3D printing requires a different skill set, which can be overwhelming for some.
Computer-Aided Design
Computer-Aided Design (CAD) is another significant advancement that has flooded the jewelry industry. It allows designers to create highly detailed digital models of their pieces, which can be modified and manipulated before any material is actually cut. This flexibility makes it much easier to play with shapes and effects that wouldn't possible through hand carving.
The key here is the rapid iteration; jewelers can tweak their designs instantly based on feedback or their own creative insights. CAD is popular with designers due to its ability to produce realistic renderings and comprehensive specifications for production.
Nevertheless, the tech also comes with its challenges. Mastering CAD software can take considerable time and effort. Additionally, there's always a risk of losing the personal touch that handcrafting provides. The blend of traditional techniques and modern technology needs careful balance to retain the soul of jewelry making.
Sustainable Practices
Eco-Friendly Materials
The shift towards eco-friendly materials highlights a growing awareness of environmental responsibility in jewelry-making. These materials typically use non-toxic compounds and are often sourced sustainably, reducing the ecological footprint. A significant advantage of using eco-friendly options is how they can appeal to conscientious consumers, who are becoming increasingly wary of the environmental impacts of their purchases.
For example, utilizing recycled metals or ethically sourced gemstones not only meets modern consumer demand but also serves as a statement of the craftsperson's values. Yet, finding quality eco-friendly materials can be challenging. Some artisans may struggle to balance the aesthetics or durability of these materials against their ecological benefits.
Waste Reduction Techniques
Waste reduction techniques represent an essential part of innovating in wax molding. These techniques aim to minimize surplus material during the jewelry creation process. Efficient use of wax and metal can significantly decrease waste, aligning with the principles of sustainability.
One effective method includes reusing wax scraps to form new models, hence conserving resources while fostering creativity. This approach not only saves costs but also enhances the artistic aspect of the craft, as every piece of material can find a new purpose.
However, implementing waste reduction practices involves a paradigm shift in how some jewelers traditionally operate. The learning curve can be steep, and some may need support and resources to successfully adapt.
Innovations in wax molding techniques are not just about incorporating new tools; they represent an evolution in artistry and responsibility in the jewelry industry.
The Future of Wax Molding in Jewelry
As we gaze into the crystal ball of jewelry design, it becomes clear that wax molding is not just a relic of the past; it represents a vibrant future. The melding of traditional craftsmanship with modern technology is making waves in the jewelry world, offering new opportunities that were previously unimaginable. In this section, we will explore trends in demand, customization options, niche markets, mentorship, and the vital need for preservation of techniques.
Trends and Market Demand
Customization
The aspect of customization in wax molding stands out like a diamond in the rough. With consumers increasingly seeking pieces that reflect their personal stories, customized jewelry has found its home in this art form. This characteristic of personalization is a game-changer because it empowers both the jeweler and the client. Each piece isn't just an accessory; it becomes an extension of an individual's identity.
Customizable options may include variations in design, choice of materials, and even the incorporation of sentimental gemstones. The upside? This trend boosts customer engagement and satisfaction, ensuring that each piece is both unique and meaningful. However, a downside can be the longer lead times for production, which some customers may find frustrating.
Niche Markets
Niche markets are another exciting avenue in waxing and molding. This aspect allows jewelers to cater to specific interests, from eco-conscious consumers to tech enthusiasts who might be captivated by pieces that combine artistic value with modern flair. The lure of niche markets lies in their specificity — jewelry designers can target select groups, creating pieces that resonate on a deeper level.
For example, there’s a burgeoning market for sustainable jewelry crafted from recycled wax and eco-friendly materials. This approach not only attracts conscientious buyers but also aligns with the growing global emphasis on sustainability. Nevertheless, focusing solely on a niche can limit market reach. Therefore, artisans must balance specialization with broader market trends.
Legacy of Craftsmanship
Mentorship in the Craft
Mentorship plays a crucial role in sustaining the legacy of wax molding techniques. When experienced artisans share their knowledge and skills with newcomers, it creates a bridge of tradition and innovation. This process is not just beneficial but is a vital survival mechanism for complex techniques that risk fading away. The guidance from seasoned professionals aids in refining the skills of apprentices, imbuing them with both technical prowess and an appreciation for the craft's history.
However, mentorship isn't a one-way street. For mentors, it brings a fresh perspective from eager minds, fostering creativity and possibly even reinventing age-old methods to suit contemporary needs. Without a doubt, the symbiotic relationship between mentor and mentee enhances the jewelry-making field.
Preservation of Techniques
Preserving techniques in wax molding jewelry is paramount, like keeping precious secrets safe. The art of wax molding is centuries old, and its techniques, ranging from traditional to modern, warrant safeguarding. By documenting these techniques, artisans ensure that even future generations have access to the foundational skills that shape this craft.
Methods of preservation can include everything from workshops that teach these techniques to online courses that make learning accessible. There's a sense of responsibility that comes with sharing knowledge, ensuring that each generation of jewelers hones their craft with integrity. However, the challenge lies in balancing preservation with the infusion of new ideas — too rigid an adherence to traditional methods might stifle innovation.
In summary, the future of wax molding jewelry is nestled in the arms of innovation and tradition, moving forward with a strong focus on customization, niche markets, mentorship, and preservation of age-old techniques.
Ultimately, understanding these components will not only enlighten the heirlooms of tomorrow but will also cultivate a deeper appreciation among gemstone enthusiasts, collectors, and jewelry designers alike.
Culmination
The importance of the conclusion in this article lies in its ability to tie together the intricate threads of wax molding jewelry, illuminating the depth and breadth of the subject. This final section encapsulates key insights from the preceding discussions—drawing connections between the historical significance and modern applications of wax molding techniques.
Summarizing Insights
In summary, wax molding jewelry is not just a craft; it is an art form intertwined with science. The precision and versatility offered by various types of wax empower artisans to push boundaries in their designs. They can create intricate models that are both aesthetically pleasing and functionally sound. This practice stands out because it combines both traditional craftsmanship and contemporary innovation, demonstrating that artistry is still grounded in technique.
- Artisan Techniques: From the early methods to state-of-the-art technology, each technique carries its legacy.
- Material Significance: The choice of wax directly impacts the final product, influencing both durability and detail.
- Market Trends: As customization grows in demand, the opportunities for jewelers are expanding swiftly, allowing them to carve out niche markets.
Understanding these elements cultivates a deeper appreciation for the artistry and meticulous effort that goes into every piece, underscoring the notion that each creation tells a story shaped by the hands of its maker.
Encouragement for Future Artisans
For those considering entering the realm of wax molding jewelry, the journey is both challenging and deeply rewarding. Each effort, no matter how small, contributes to skill development and pushes creative boundaries.
- Embrace your unique style and be bold in experimentation.
- Share your work with communities online, such as platforms like Reddit, where feedback and support abound.
- Pursue learning through mentorship programs or workshops, leveraging the experiences of seasoned jewelers, who often highlight the importance of learning from one's mistakes.
Remember, every great artisan started as a novice. It is the passion and willingness to refine one's craft that will ensure your place in the intricate tapestry of jewelry making. Wax molding offers a pathway to express individuality and leave a mark in this vibrant space.