Essential Stone Cutting Tools for Jewelry Making

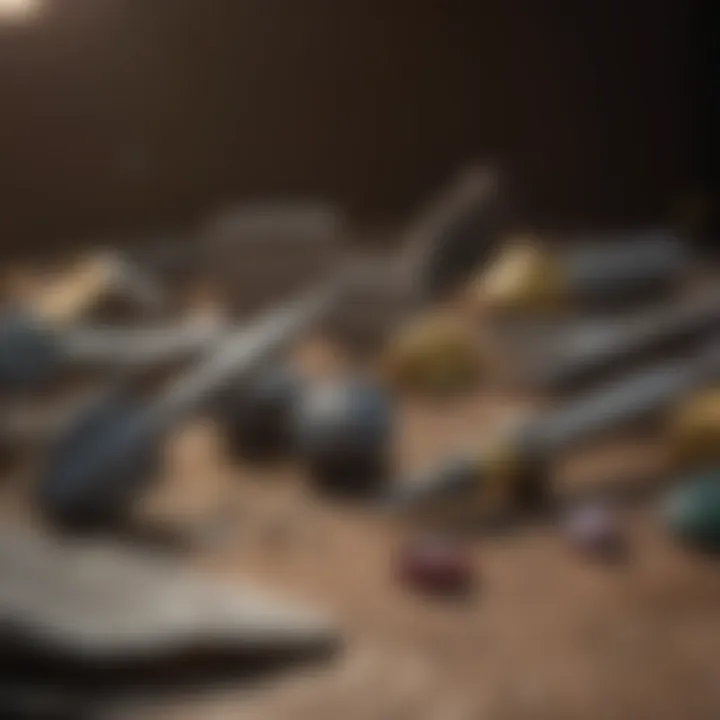
Intro
In the fascinating world of jewelry making, stone cutting is an art that takes considerable skill and the right tools. As a gem enthusiast wants to delve into creating bespoke pieces, understanding the tools at one's disposal is paramount. Selecting the right equipment can make or break your craftsmanship, influencing everything from the stone's appearance to the safety of your work environment. In this guide, we will navigate through the essential tools needed for stone cutting, explore their purposes, and provide insights on techniques and best practices.
Through this journey, we will also look at the properties of gemstones themselves, a fundamental aspect that informs how they should be cut and shaped. Both budding jewelry makers and seasoned crafters can benefit from a closer examination of these tools and techniques. Whether you’re looking to make a statement piece or delicately refined accessories, understanding how to wield your tools with precision can lead to creations that are not only beautiful but also durable and unique. Let's begin our exploration by moving into the characteristics and classifications of gemstones.
Intro to Stone Cutting in Jewelry
Stone cutting has long been the backbone of jewelry making, transitioning raw stones into exquisite, wearable art. This process is not just about aesthetics but intricately linked to the value and durability of gemstones. For jewelers, understanding the significance of stone cutting is key. It involves applying specific techniques and using specialized tools that enhance the beauty of stones while preserving their integrity.
A well-cut gemstone can dazzle under any light, revealing depth and brilliance that raw stones simply do not possess. The importance of stone cutting isn't only in artistry; it also dictates clarity, color, and overall appeal. Jewelers who ignore this element often end up with stones that are less desirable, regardless of their raw material's quality.
In this journey of transforming unrefined stones into stunning pieces, various factors come into play:
- Creative Expression: Each stone offers a unique opportunity for artistic expression. How a stone is cut can change a design entirely.
- Market Value: Well-cut stones command higher prices. Their brilliance and craftsmanship tend to attract buyers.
- Durability: Proper techniques can bolster a gem's durability. A knowledgeable cutter knows how to work with each stone's properties, ensuring longevity.
The foundations of jewelry design lie within understanding different types of stone and how cutting can influence each one. Thus, delving into the adjacent facets of stones will provide jewelers with a comprehensive guide to horning their craft.
The Importance of Stone Cutting
Stone cutting is vital for several reasons. First, it serves the fundamental purpose of shaping a stone for practical use. Without cutting, rough stones would merely be decorative pebbles with little to no allure. Moreover, cutting makes stones more manageable during the jewelry creation process.
A properly cut stone can showcase the nuances of color, light, and clarity that each gem possesses. Consider how diamonds, when cut in particular shapes like round or princess cuts, offer sparkle that catches the eye and elevates the gemstone's intrinsic beauty.
Additionally, the craftsmanship involved in stone cutting often reflects the skill and knowledge of the jeweler, setting professionals apart in a crowded market. For example, an experienced cutter can impart a charm to a piece that harmonizes with the wearer’s personality or fashion.
Overview of Stone Types Used in Jewelry
In the vast world of gemstones, there are many varieties used in jewelry making, each requiring different considerations in stone cutting. Common stones include:
- Diamonds: Renowned for their brilliance, they are cut to maximize how they reflect light. Understanding the properties of a diamond is essential for a successful cut.
- Sapphires: These come in various colors, and their cutting enhances their vividness. There’s both artistry and technicality involved – a delicate balance that jewelers must master.
- Emeralds: Often cut in a rectangular shape to highlight their stunning green. Their crystalline structure requires a gentler touch.
- Quartz: With numerous variations such as amethyst or citrine, they are easier to cut, allowing for more creativity.
- Opals: Unique for their play of color, cutting techniques for opals may vary significantly to preserve their unique patterning.
"Stone cutting goes beyond mere technique—it's about understanding the life within the stone and the vision of the craftsman."
Each type of stone contributes its own narrative to the jewelry being crafted. By delving into the specifics of stone types, aspiring jewelers can better appreciate the finer details of their practice, such as optimal cutting methods and design concepts.
Basic Stone Cutting Tools
The yin and yang of jewelry making often hinges on the tools used to cut and shape stone. Each tool serves a fundamental purpose in the expansive world of gemstone crafting; thus, knowing which ones to utilize can make or break the quality of the final piece.
In this section, we will dissect various stone cutting tools, drawing attention to both hand tools and power tools. Understanding these tools isn't just about their existence; it's about grasping their intricacies and the influence they exert over different cutting techniques. Whether you're shaping a cabochon or preparing a diamond for faceting, the right instrument will bring out the best in your work.
Preface to Cutting Tools
Cutting tools are the backbone of any stone cutting project. They come in many shapes and sizes, tailored to specific tasks. From manual options that rely on the jeweler's skill and precision to power tools that speed up the process with finesse, each category delivers its own set of advantages.
These tools help in achieving the desired shape, texture, and polish of the gemstone. A clear understanding makes it easier for jewelry makers to navigate the vast tool landscape, ensuring they select the right one for each distinct task.
Hand Tools
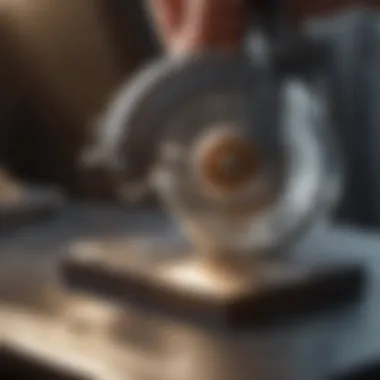
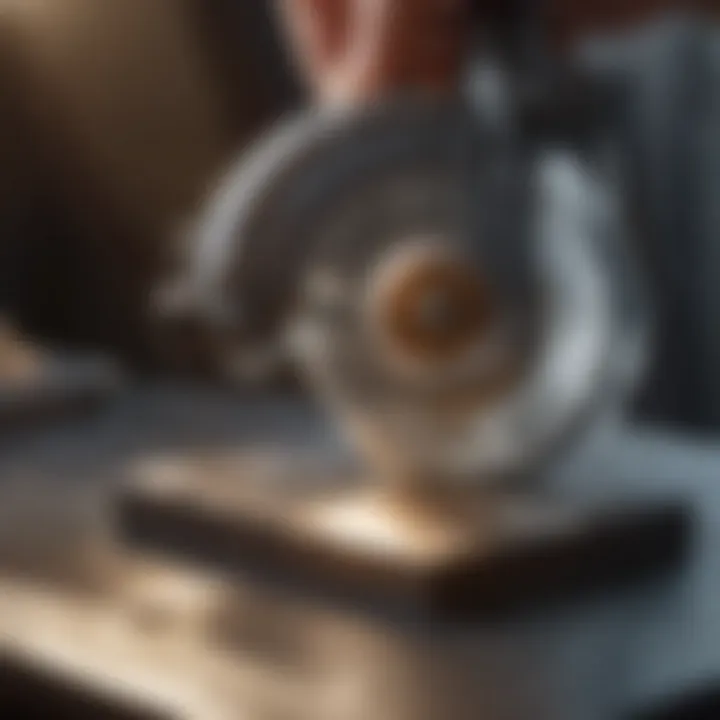
Diamond Saw Blades
In the realm of stone cutting, diamond saw blades stand out for their cutting efficiency. Designed with industrial-grade diamonds embedded into their edges, they slice through hard materials with ease. The key characteristic of these blades is their durability; they can tackle anything from softer stones like quartz to the hardest diamonds.
What sets diamond saw blades apart is their unique feature: the continuous rim. This design enables smoother cuts, minimizing chip-off and providing a clean finish. However, it's worth noting that while these blades are immensely effective, they come with a higher price tag, reflecting their quality and performance.
Files and Rasps
Files and rasps provide the necessary finesse to jewelry making. Their primary role is to refine shapes and smooth out rough edges or surfaces after the initial cuts. The important aspect here is their granulation. Files tend to have finer teeth, while rasps are coarser and ideal for removing more material quickly.
Their key advantage lies in their ability to give intricate detail to the work. Though they require manual effort and patience, they're relatively inexpensive and can be a go-to choice for many jewelers, especially when crafting intricate designs.
Grinders
Grinders are the powerhouse tools that aid in polishing and shaping stones to a fine finish. They come in various forms, such as belt grinders and wheel grinders, each serving a unique purpose. The standout feature of grinders is their versatility; they can tackle a variety of materials, adjusting to different shapes and sizes.
While grinders can significantly speed up the process of shaping stones, one must handle them with care. They're powerful and if mismanaged, can easily damage a gemstone, which becomes a disadvantage for those still mastering their technique.
Power Tools
Rotary Tools
Rotary tools are the Swiss Army knives of stone cutting. Equipped with various attachments, they can handle tasks ranging from drilling to carving and grinding. Their versatility is a strong selling point; you can switch between tasks without the need for multiple tools.
One unique feature is the adjustable speed settings, enabling jewelers to fine-tune their approach based on the material being worked on. However, over-reliance on rotary tools can lead to a loss of control, hence the need for practice and attention.
Lapidary Machines
Lapidary machines are specifically designed for gemstone cutting and polishing. This power tool is built for precision, often incorporating multiple stages like cutting, grinding, and polishing in one mechanism. The continuous use of water or coolant during the process reduces heat buildup, protecting the integrity of the stone.
Their main advantage is the maximized efficiency in transforming rough stones into polished gems within a streamlined workflow. On the flip side, initial set-up and investment can be costly for beginners.
Saws and Trim Saws
Saws and trim saws are vital for making the initial cuts in larger stones. Standard saws often handle bulk material, while trim saws manage delicate work, providing the precision needed for intricate design. The key characteristic is their blade sharpness and segmentation, which can tackle both hard and soft materials effectively.
What’s unique about these saws is their adaptability. Users can choose blades based on the type of cut desired. However, as with any power tool, they come with a learning curve; mastering the saw's control is essential to prevent any mishaps.
"The right tools amplify your capabilities as a jeweler, enabling you to turn raw ideas into tangible art."
Advanced Cutting Techniques
Advanced cutting techniques are at the heart of elevating the craft of jewelry making. Mastering these methods not only enhances the quality of the final product but also unlocks a world of creative possibilities. The implementation of sophisticated cutting techniques can significantly affect the visual appeal and intrinsic value of gemstones. Understanding these advanced methods can set a jeweler apart, enabling them to produce unique pieces that reflect their artistry.
Understanding Faceting
Faceting is a process where flat surfaces, called facets, are created on the surface of a gem. This technique is more than just a method of cutting; it’s a dance of angles that determines how light interacts with the stone. Faceted gems refract light in fascinating ways, creating a play of brilliance that often captivates onlookers.
The importance of faceting lies in its ability to maximize a gemstone's light performance. A well-faceted stone can exhibit more sparkle and fire. For example, a high-quality diamond, when cut with precision, can return more light to the viewer than a poorly faceted counterpart, even if both stones are of equal size. Key considerations in faceting involve the choice of angles and proportions, which require a deep understanding of optical principles. Jewelers often rely on faceting machines for accuracy, but the essence of skill lies in the eye of the cutter.
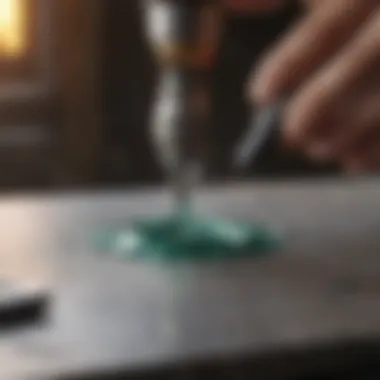
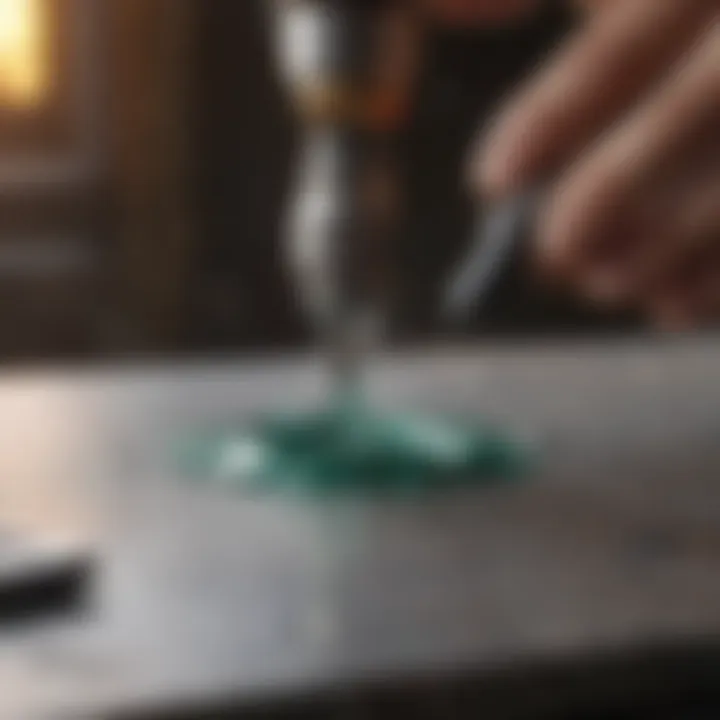
Cabochon vs. Faceted Cuts
The choice between cabochon and faceted cuts can deeply influence the character of a stone. Cabochon cutting involves shaping the gemstone into a smooth, rounded dome rather than using angles to create facets. This technique enhances the color and pattern of opaque stones like turquoise or jade, showcasing their natural beauty without the interference of light dispersion. Some of the greatest advantages of cabochon cuts include:
- Simplicity: It allows the inherent features of the stone to shine without distraction.
- Ease of Handling: With fewer angles than facet cuts, cabochons can be easier to work with for beginners.
On the flip side, faceted cuts are perfect for stones where brilliance and light reflection play a crucial role, like diamonds or sapphires. The decision ultimately hinges on the intended purpose of the jewelry piece and the inherent properties of the stone. The distinct outcomes of these two techniques exemplify the range of expression possible in stone cutting:
- Cabochon cuts often impart a rustic charm and emphasize color and texture.
- Faceted cuts can bring out dazzling brilliance and complexity, appealing to the eye's fascination with light.
"Choosing the right cut can transform the ordinary into the extraordinary."
In summary, both cabochon and faceted cuts play crucial roles in the realm of jewelry making. Each offers unique advantages tailored to different types of gemstones, highlighting the need for jewelers to be well-versed in advanced cutting techniques to ensure their creations captivate the audience.
Essential Skills for Stone Cutting
The art of stone cutting in jewelry making isn't just about having the right tools at hand; it hinges significantly on a few key essential skills. These skills elevate a jeweler's ability to transform raw gemstones into stunningly crafted pieces, each reflecting their unique artistry. Understanding these crucial components not only enhances the quality of the finished product but also deepens the craftsperson's appreciation for the material they work with. Developing proficiency in stone cutting results in greater enjoyment and, ultimately, success in jewelry making.
Precision and Patience
Precision in stone cutting goes beyond mere accuracy; it requires a steady hand, keen eye, and careful thought process. Jewelers need to measure, mark, and execute cuts with meticulous attention to detail. A small oversight can alter the shape or integrity of the stone, resulting in subpar outcomes or even ruining a valuable gem. Thus, the necessity for precision cannot be overstated.
On the other hand, patience in this craft is equally critical. Jewelers often face hours of grinding, polishing, and refining their workpiece. Rushing through these steps can lead to mistakes that might be regrettable later. Each stroke of a tool should be deliberate, reflecting the jeweler’s dedication to quality. In a world where instant gratification seems to dominate, nurturing patience can feel like a rarity but is essential when cutting stones—good things take time.
Eye for Detail
An impeccable eye for detail is what separates a good jeweler from a great one. The smallest variations in a stone's surface or structure can impact its overall beauty and market value. Being able to notice these nuances requires experience, yet it can also be cultivated over time. For example, noticing the way light refracts within a stone may influence not just the cutting technique but also the intended design.
What’s more, having a discerning eye allows jewelers to spot potential issues before they escalate. A careful inspection of gemstones can identify flaws or inclusions that might necessitate a different cutting approach. As the saying goes, “The devil is in the details,” and having this keen observation skill can truly enhance the final product.
Understanding Stone Properties
Knowing the properties of different stones is essential for any jeweler. Each gemstone varies in hardness, clarity, cleavage, and other characteristics that influence how it should be cut. For instance, softer stones like talc will require gentler handling to avoid damage, while harder gems like diamonds may allow for more aggressive cutting techniques.
Understanding the unique qualities of stones aids in selecting the right tools and methods for cutting and shaping. Having this foundational knowledge is akin to knowing the instrument one plays—misunderstanding the nuances could lead to disastrous misplays, so to speak. Jewelers can also experiment creatively with different stone properties to create novel designs that stand out.
"Knowing your material—its strengths, weaknesses, and quirks—is half the battle; the other half lies in how you choose to shape it.”
Cultivating these essential skills in stone cutting not only ensures a jeweler's work meets a high standard but also augments their creativity. A jeweler who invests time in honing precision, developing a sharp eye for detail, and understanding stone properties, will undoubtedly see the qualities of their work reflect their knowledge and dedication, ultimately delighting collectors and enthusiasts alike.
Safety Considerations in Stone Cutting
When it comes to working with stone, particularly in jewelry making, safety is not just an afterthought; it’s the bedrock of every successful project. The process of cutting and shaping stones brings together fine craftsmanship and precision, but it inherently carries risks. These risks can be mitigated with proper safety protocols and equipment.
Using suitable protective gear and understanding how to store and handle tools safely can significantly reduce accidents. It’s not merely suggested—it's essential. Following a few key safety practices enables artists to focus on their creativity rather than worrying about potential injuries.
Protective Gear
Goggles
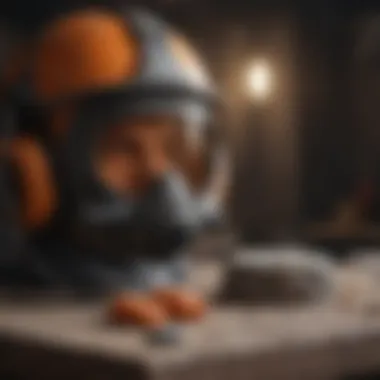
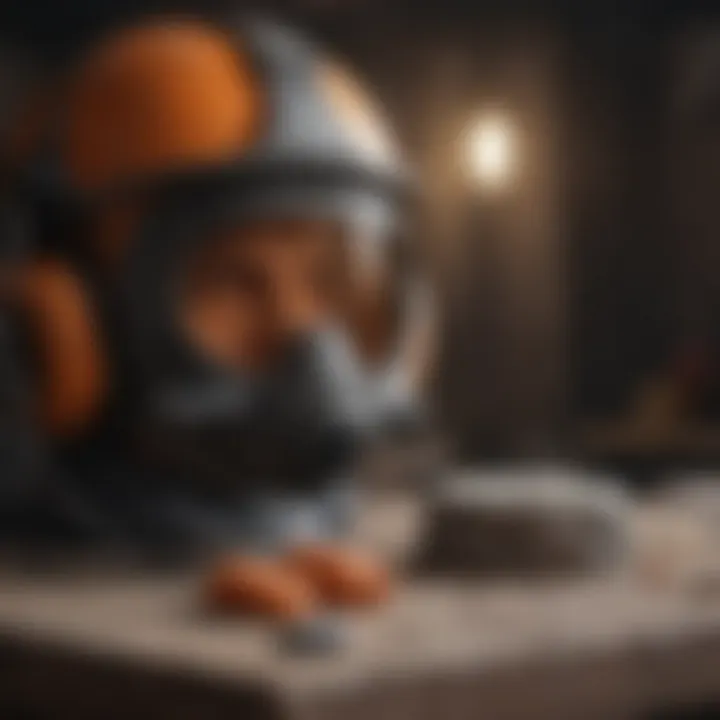
Goggles are a crucial part of your stone-cutting arsenal. They protect the eyes from debris flying off during cutting. One key characteristic of goggles is their snug fit, ensuring that no small particles can seep in from the edges. This characteristic makes them an extremely wise choice for anyone working with power tools or even hand tools like saws and chisels.
A unique feature to consider in goggles is anti-fog technology, which can be a game-changer in maintaining clear visibility while working. The advantage here is straightforward: you can see your work without intermittently wiping off fog. However, some goggles may compromise peripheral vision, which could be a disadvantage when you need to keep an eye on the work area.
Gloves
Gloves are indispensable when handling sharp tools and rough materials. A vital aspect of gloves is the protection they offer against cuts and abrasions. Selecting gloves made from durable materials, such as leather or synthetic composites, is essential. These materials provide a good grip while shielding your hands from jagged edges and sharp shards.
One unique benefit of gloves is their ability to absorb vibrations when using power tools, contributing to comfort and safety. Disadvantages can include decreased tactile sensation, making it harder to feel smaller tools or make delicate adjustments when necessary. Nonetheless, the trade-off is often worth the peace of mind that comes from knowing your hands are protected.
Respirators
Respirators play a key role in ensuring lung safety while cutting stone. The nature of stone dust is such that it can be hazardous if inhaled over prolonged periods. A primary characteristic of effective respirators is their filtration system, often rated to filter out very fine particles and harmful substances. This makes them particularly beneficial for jewelers who work with various materials that can produce harmful dust.
A unique feature to look for in a respirator is a snug-fitting, adjustable design, which enhances comfort and effectiveness. However, while respirators offer significant protection, they may be uncomfortable for extended wear, particularly for those unaccustomed to using them. Still, when considering the health risks involved, using a respirator is a responsible choice for any stone worker.
Storage and Handling of Tools
Proper storage and handling of tools are crucial. Tools should be kept in dedicated spaces that allow easy access while minimizing the risk of spills or falls. A simple layout, such as a toolbox with compartments, helps keep everything organized.
When handling any tool, it’s vital to be mindful of posture and movement. For instance, bending at the knees rather than the waist reduces strain and promotes better control. Also, proper handling techniques can significantly contribute to both personal safety and tool longevity.
Emerging Trends in Stone Cutting Tools
The world of stone cutting in jewelry making is continuously evolving, driven by technological advancement and the ever-growing demands of artisans. Keeping an eye on emerging trends is crucial, as they not only enhance craftsmanship but can also bolster efficiency and creativity. By exploring these trends, jewelers can harness new capabilities that refine their art and business strategies, ensuring they're not just keeping pace but setting the standard in the industry.
Innovations in Diamond Technology
Diamond technology has seen remarkable progress lately. Historically, diamonds were only understood as the hardest materials available. However, recent developments enabled the creation of synthetic diamonds like those produced by companies such as De Beers' Lightbox. These innovations provide artisans the opportunity to work with stones that have consistent quality and less environmental impact.
Moreover, the introduction of laser-cutting methods has sparked a transformation in how diamonds are shaped and polished. With precision that was unimaginable years ago, professionals can create intricate designs that catch light in mesmerizing ways. Diamond-edge tools are becoming prevalent in cutting circles, offering jewelers better performance while also prolonging tool life.
The leap from traditional techniques to modern methods not only brings efficiency into the workshops, it empowers jewelers to express their vision without boundaries.
Computer-Aided Design (CAD) Integration
In the age of digitalization, the integration of Computer-Aided Design (CAD) is changing the jeweler's workspace. CAD software allows for detailed designs to be visualized before the cutting begins—imagine working on a digital canvas that saves both time and materials. Jewelers can manipulate shapes, colors, and details in real-time, which drastically improves their workflow.
Moreover, CAD files can be sent directly to 3D printers, enabling the creation of prototypes to test before committing to a final design. As the technology advances, it's likely we'll see an expansion in the types of materials that can be used, further broadening artistic possibilities. Jewelers who embrace CAD not only streamline their production but also attract a customer base interested in personalized and intricate work.
Utilizing CAD in jewelry-making is akin to wielding a magic wand—what once took weeks of trial and error can be achieved in a matter of hours.
Lastly, the blend of CAD with augmented reality (AR) is on the horizon, allowing clients to visualize how a piece will look on them or in their home—an innovation that could redefine the customer experience.
The combination of these emerging trends not only signifies where the jewelry-making industry is headed but also creates an opportunity for artisans to elevate their craft while ensuring they remain adaptable and competitive in a rapidly changing marketplace.
Culmination
In wrapping up our exploration of stone cutting tools tailored for jewelry making, it's crucial to underscore the pivotal role these instruments play in the craft. Jewelers and gemstone enthusiasts aren't just manipulating raw materials; they are transforming nature's gems into objects of desire and beauty.
The Future of Stone Cutting Tools
As we look toward the horizon of jewelry making, the advancements in stone cutting tools reveal a landscape ripe with possibilities. The integration of various technologies is not just reshaping how stones are cut but also how artisans approach their craft.
- Innovative Materials: The future promises the usage of newer composite materials, enhancing durability and efficiency.
- Smart Technologies: With the rise of smart devices, imagine tools that can analyze stone properties in real-time, suggesting the most effective cutting techniques for specific gemstones.
- Sustainability: Increasingly, the industry is focusing on environmentally friendly practices, with tools being designed to reduce waste and promote sustainable sourcing.
Exploring these trends not only helps jewelers stay ahead of the curve but also fosters a deeper appreciation for the artistry involved in making jewelry.
This progression towards advanced technology and sustainability illustrates a broader commitment to innovation while preserving the essence of craftsmanship that has defined jewelry making for centuries. Each milestone in this journey reflects the ongoing relationship between material science, artistic creation, and responsible stewardship of resources.
As we navigate through these changes, it becomes clear that understanding the tools and techniques of stone cutting is more than a practical requirement; it’s essential for anyone looking to excel in the field.